Холдингу МПРК «ГРАС» принадлежат 2 завода по производству автоклавного газобетона: в п. Александровка Саратовской области, и г. Светлоград Ставропольского края, совокупно выдающие в год более 900000м³ блоков под аналогичной торговой маркой. Несмотря на пандемию и политическую обстановку последних лет, цены и объёмы производства газобетона ГРАС сохраняют стабильность - и, что немаловажно, достойное качество. Соответственно, спрос на материал, о котором мы здесь и расскажем, только возрастает.
О технологии производства
Оба завода, выпускающие газоблоки ГРАС, оснащены голландской технологической линией Hess AAC Systems B.V. Это надёжный производитель строительного оборудования с мировым именем, а хорошее оснащение – залог получения качественного продукта. Рассмотрим вкратце, как изготавливают автоклавные газоблоки, и какими методами достигаются нужные характеристики.
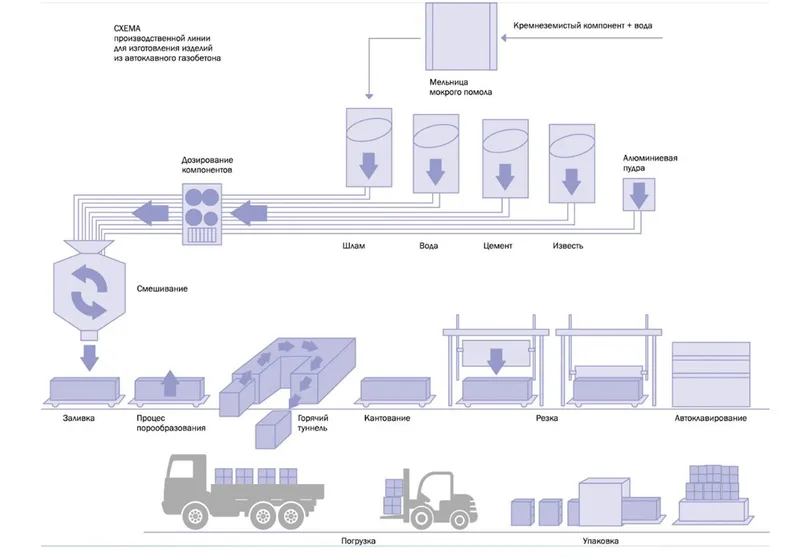
Сырьё для производства, его подготовка и замес
В качестве связующего компонента в производстве газоблоков (речь идёт об автоклавном продукте), применяется не только цемент, но и известь. Реакция синтезирования требует увеличенного количества кальция - при высоких температурах он взаимодействует с кремнезёмом, образуя гидросиликат (тоберморит), за счёт которого и повышается класс прочности бетона без увеличения его плотности.
- Когда бетон изготавливается только на цементе, в его состав приходится вводить добавки с высоким содержанием кальция – например, тонкомолотую золу уноса. Известь же сама по себе богата кальцием, и может служить не просто добавкой, но и основным вяжущим.
- Основным, но не единственным, потому что цемент тоже добавляется для прочности. Именно на комбинированном вяжущем изготавливают газобетон на заводах МПРК «ГРАС». Так как доля порошковой извести в сырьевых смесях больше, чем доля цемента, газоблоки называются газосиликатом. Визуально их можно отличить от цементных блоков по более светлому оттенку серого, или почти белому (конкретный цвет зависит от пропорций вяжущего).
Визуальное отличие газосиликатного блока от цементного
- Известь и цемент производители хранят в предназначенных для сыпучих материалов силосах. Песок, доля которого в составе газобетона является самой большой, складируется на складах с открытыми площадками.
- Четвёртым сухим компонентом газобетона является двуводный гипс - твёрдый кристаллический природный минерал, применяемый в качестве добавки. С её помощью регулируют время набора пластической прочности, а так как в гипсе тоже содержится кальций, такая добавка благоприятно влияет и на конечную прочность камня.
- Если гипс поставляется в виде порошка, его просто просеивают и отправляют в замес. Комковой гипс сначала перемалывается в шаровой мельнице вместе с песком, и затворяют тёплой водой для получения жидкого шлама (плотность 1,7 кг/л). Расход шлама примерно такой: 1,5 тн на 1м³ газобетона.
- Готовый шлам закачивается в бассейны, оснащённые электрическими мешалками, откуда через дозатор подаётся в смеситель. Замес производится в усредняющем баке, туда же с помощью насоса добавляется водная суспензия алюминиевой пасты. Точное соблюдение дозировок компонентов согласно рецептуре отслеживается автоматической системой управления.
Компонентный состав автоклавного газобетона
Обратите внимание: Производитель технологической линии компания HESS запатентовала систему, благодаря которой порошковые материалы можно перемещать самотёком, обходясь без конвейеров.
- Готовую смесь заливают в прямоугольные опалубочные формы размером 6160*1580*690 мм (длина*ширина*высота), с одним съёмным бортом. Уровень заполнения формы может быть разным, в зависимости от плотности бетона, которую необходимо получить, но в среднем составляет 350 мм.
- С запуском реакции газообразования смесь начинает вспучиваться и расти в объёме, так что в итоге форма окажется заполненной до краёв. Длится брожение порядка 30 минут, в течение которых в массиве будущего бетона и формируются ячейки.
Чтобы образование пор происходило равномерно, на смесь кратковременно воздействуют высокочастотными игловыми вибраторами. После этого массив оставляют в покое на 2,5 часа, в течение которых он набирает структурную прочность, позволяющую производить последующие действия.
Выемка из форм, нарезка массива на блоки
Выдержанный массив, набравший определённую твёрдость, перемещается манипулятором к месту раскроя – а чтобы бетон не охладился, его для поддержания температуры пропускают через горячий тоннель. Затем форму устанавливают на съёмный борт: он автоматически отстёгивается, а остальная часть корпуса опалубки снимается и возвращается к площадке созревания, где она будет смазана и подготовлена для новой заливки.
Монолит же движется дальше к резательной линии, где проходит такие стадии обработки:
- предварительная разметка ножами;
- снятие горбушек и выравнивание граней триммером;
- вырезание захватных карманов по торцам;
- раскрой монолита в размер блоков: сначала горизонтальная, а затем поперечная резка, с применением струн пневматического натяжения.

Оборудование HESS настраивается настолько тонко, что позволяет произвести раскрой массива на блоки даже с меньшими отступлениями от номинала, чем позволяет ГОСТ 31360-2007. Образовавшиеся в процессе раскроя обрезки сбрасывают в шламовый канал, и с потоком воды отправляют в шаровую мельницу на переработку. Так образуется вторичный шлам, который вновь поступает в производство - соответственно, неиспользуемых отходов здесь нет вообще.
Автоклавная обработка, складирование продукции
Всё ещё находящийся на снятом с опалубки бортике, монолит укладывается на решётчатый поддон и перемещается в зону разделения, где по нарезанным линиям блоки отделяются друг от друга, чтобы не слиплись. Затем производится погрузка на вагонетку, куда помещается три таких поддона, и транспортируется к тупику. Когда набирается нужное количество вагонеток (обычно не более семи), их загоняют в тоннель автоклава.
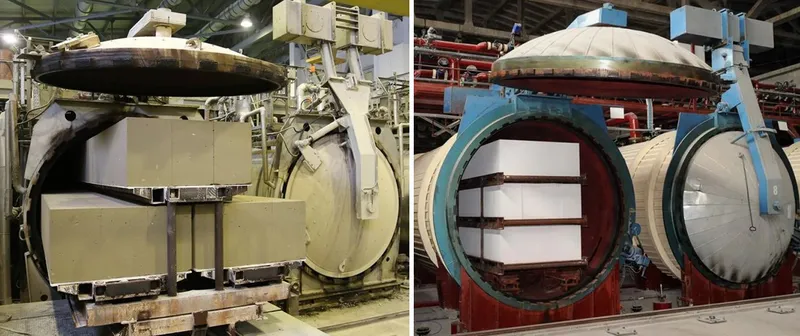
Для получения блоков той или иной плотности и прочности требуется разное количество времени, но в среднем газобетон подвергается паровлажностной обработке в течение 12 часов. При закрытии дверцы автоклава в нём создаётся вакуум, после чего начинается постепенное наращивание температуры до +190 С, и давления до 1,2 МПа.
Продолжается нагнетание в течение 6 часов, после чего начинается столь же постепенный выход из режима синтезирования. При достижении оптимально низкой температуры, крышку тоннеля открывают, а вагонетки выталкивают наружу. Вместе с решёткой манипулятор перемещает блоки к зоне разгрузки, где их укладывают на паллеты и затягивают штабели термоусадочной плёнкой.
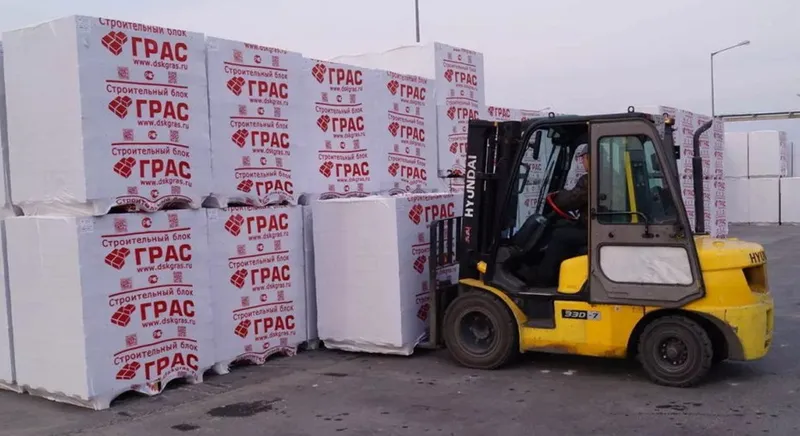
Примечание: Количество блоков на поддоне в кубометрах составляет 1,875 -2,16м³, но количество штук зависит от их размера. Например, стеновых блоков 625*375*250 мм в стандартный поддон помещается 32 штуки, а перегородочных 625*100*250 мм – 120 штук.
Стрейч-плёнка не только уберегает блоки от загрязнения и намокания под дождём, так как поддоны хранятся на открытых складских площадках, но и служит готовому продукту этикеткой, где указан бренд и адрес сайта производителя.
Обзор газобетонной продукции
Домостроительные комбинаты ГРАС выпускают блоки для возведения стен и перегородок, устройства вентиляционных каналов (О-блоки) и несъёмной опалубки для армопоясов (U-блоки).
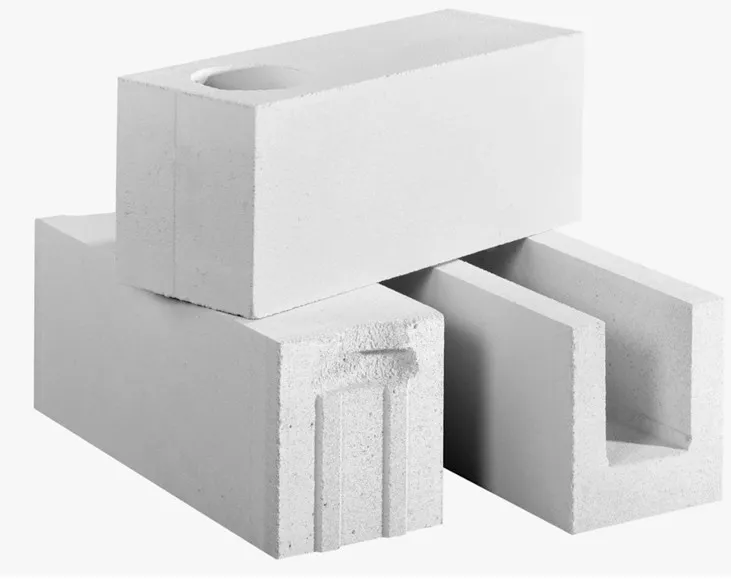
Так же потребителю предлагаются: газобетонные армированные перемычки; газобетонный щебень для утепления чердаков и полов; минеральная кладочная смесь и клей ППУ; кладочная сетка; ручные приспособления, необходимые для кладки и механической обработки блоков.
Блоки для несущих стен
Основным продуктом являются, конечно, стеновые блоки, и вот какими геометрическими параметрами они обладают:
Внешний вид блока | Марка по плотности | Класс прочности на сжатие | Параметры блоков (мм) | ||
Длина | Высота | Ширина | |||
![]() |
D 300 | В2 | 600 | 400 | 100 и 150 |
D 350 | В2,5 | 250 и 200 | 100; 125; 150; 200; 250; 300; 375; 400; 450; 500 | ||
D 400 | В2,5-3,5 | ||||
D 500 | В2,5-3,5 | ||||
D 600 | В2,5; 3,5 и 5,0 | 600 | 250 и 200 | 150; 200; 250; 300; 375; 400; 450; 500 |
На производстве газоблоки обязательно подвергаются контролю качества. Кроме лабораторных испытаний, по результатам которых устанавливаются кубиковая прочность на сжатие и марки по плотности и морозостойкости, это выборочная оценка соответствия фактических размеров номиналу.
Также производится визуальный осмотр, в процессе которого блоки с нарушенными гранями, или имеющие на поверхностях разводы или перепады цвета, отбраковываются. Это не значит, что их вообще нельзя использовать в строительстве. Можно - но это уже более дешёвый продукт второго сорта, из которого во дворе можно возвести любую неотапливаемую постройку, для которой не важны теплопроводность блока и тонкость швов кладки.
Блоки саратовского завода 1 категории качества стоят 6400 руб./м³, а блоки 2 категории стоят 4600 руб./м³ (отпускные цены в феврале 2024г). Разница существенная, что позволяет неплохо сэкономить, если нужно построить гараж, курятник или теплицу.
Вспомогательные блоки
Кроме стеновых блоков при строительстве дома используются и перегородочные. Вариантов плотности у них меньше, так как здесь теплопроводность значения не имеет, а вот звуконепроницаемость межкомнатных перегородок важна, и чем выше плотность бетона, тем изоляция лучше. Поэтому для устройства перегородок блоки предлагаются только плотностью 500 и 600 кг/м³ класса прочности В2-3,5.
Длина и высота перегородочных блоков аналогична стеновым, варьируется только ширина – в пределах 75-150 мм. Тонкие блоки (75 мм), применяемые не только для планировки санузлов, но и для устройства несъёмной опалубки, делают и с плотностью 300 и 400 кг/м³. При устройстве армопоясов на наружных стенах, такие блоки выполняют функцию утеплителя, защищая от промерзания железобетонную балку.
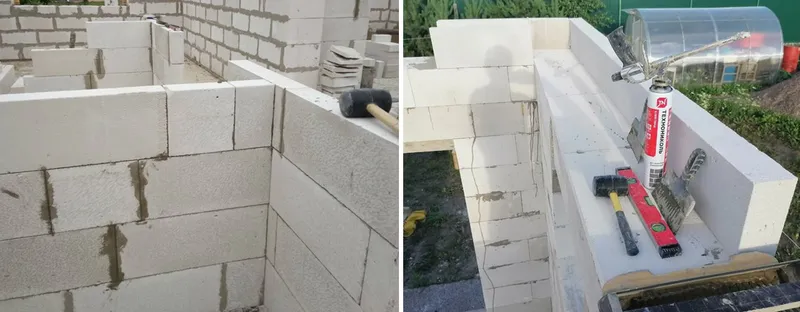
Использовать для формирования балки армопояса U-блоки, конечно, проще, чем монтировать два параллельных ряда перегородочных блоков. Но продаются они штучно по 500 руб., и цена в пересчёте на кубометр получается вдвое дороже (пара тонких блоков обходится порядка 220 руб.) Тем не менее, каждый волен выбирать: многие застройщики предпочитают использовать готовые элементы опалубки, и могут приобрести U-блоки ГРАС марки D500.
Типоразмеров не очень много – только для стен толщиной 250 и 400 мм. В остальных случаях придётся применять всё те же перегородочные блоки.
В ассортименте заводов МПРК «ГРАС» присутствует ещё изделие под названием О-блок. Это обычный по размерам блок, только имеющий сквозные отверстия для устройства вертикального армирования (в сейсмически нестабильных районах), скрытой прокладки канализационных стояков, формирования вентиляционных каналов и каминных дымоходов.
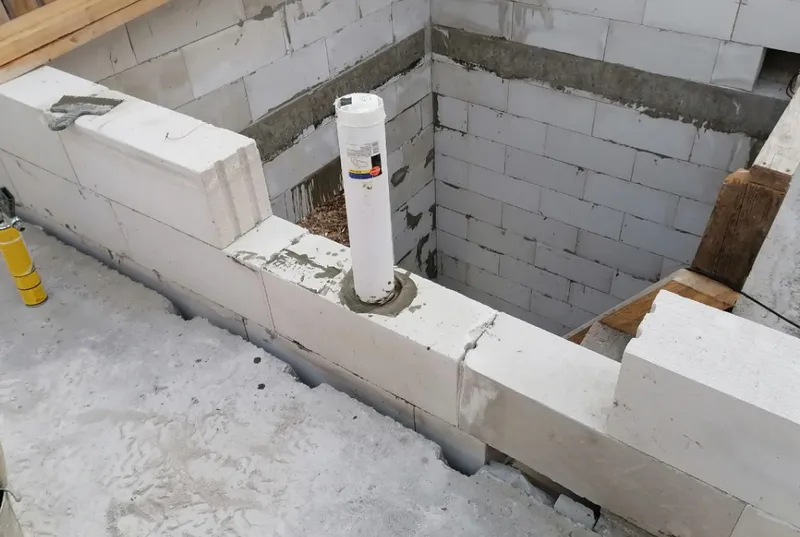
Если во внешних стенах делать каналы из плотного керамического кирпича, нарушается теплотехническая однородность газобетонной кладки - такая вставка становится одним большим мостиком холода, через который будет уходить тепло. К тому же портится эстетика фасада, ведь его далеко не всегда отделывают сразу из-за ожидания снижения влажности, или попросту ограниченного бюджета.
Особенности отделки газоблоков
Благодаря тому, что тело газобетонного камня имеет ячеистую структуру, достигается низкий коэффициент теплопроводности стен, но при этом повышается их способность пропускать через себя пар. В отапливаемых помещениях он стремится выйти наружу через ограждающие конструкции, и чтобы предотвратить конденсацию и накопление в кладке влаги, очень важно сделать этот выход беспрепятственным.
Адгезионная отделка
Обеспечить это требование можно только с помощью правильной отделки фасада. Если материал наносится адгезионно, он должен иметь такой же, как у газоблока, или более высокий коэффициент паропроницаемости (а значит, более низкую плотность). Это ограничивает выбор, поскольку клеевых отделочных материалов с такими характеристиками практически нет.
- Из тех, что есть - это декоративная плитка под кирпич и блоки с фаской под покраску, изготовленные тоже из газобетона. Их делают с плотностью 200-300 кг/м³, что ниже, чем у основной стены, поэтому проблем с паровыведением не возникает.
- Проблема в том, что такую плитку изготавливает всего один производитель, да и фрезерованные блоки тоже. Хотя идея хороша, ведь такая отделка одновременно является дополнительной теплозащитой.
Варианты отделки фасада газобетонной плиткой и блоками с фаской
- Чаще всего для внешней отделки стен используется штукатурка, потому что это и доступнее, и быстрее, и дешевле. Хотя штукатурки тоже бывают разными. Плотность любой штукатурки выше плотности газоблока, поэтому пар такое покрытие пропускает медленнее. Тут всё дело в толщине наносимых слоёв – если они тонкие, всего 2-3 мм, паробарьера не образуют.
- Из минеральных штукатурок наименьшей плотностью обладают известковые составы, в которых цемент если и присутствует, то в небольшом количестве для придания прочности, а так же силикатные, где в качестве вяжущей основы применяется жидкое стекло.
Обратите внимание: Штукатурки на обычном цементе обладают слишком высокой плотностью, но существуют микроцементные составы, в которых и цемент, и наполнитель подвергаются тонкому помолу. С их помощью выполняют покрытия под полированный бетон различных оттенков серого, бежевого или белого цвета. Смотрится такая отделка очень интересно и респектабельно, но и стоимость соответствующая.
- Для наружной отделки газобетона отлично подходят и штукатурки на синтетических смолах (латекс, силикон, акрил), которые обладают высокой способностью к паропроницанию. Обычно такая штукатурка рассчитана на достижение определённого декоративного эффекта и колеруется в массе - нанеся её, вы получаете красивый рельеф, а необходимость в поверхностной покраске отпадает.
Красиво оформленный штукатурный фасад
- Популярную в народе отделку камнем по всей площади газобетонного фасада не выполняют. Её чаще всего комбинируют со штукатуркой, акцентируя внимание лишь на подоконных зонах, узких простенках или углах, и в этом случае никакого паробарьера не образуется.
При использовании для отделки фасада клинкерной плитки, её монтаж нужно производить с широкими швами, которые для удаления пара заполняются паропроницаемой затиркой. При мелком формате плитки общая площадь швов получается значительной, поэтому процессу пароудаления ничто не мешает.
Вентилируемая отделка (на относе)
По системе вентилируемого фасада на газобетонные стены можно монтировать любой материал, так как навешивается он на подсистему, и с базовой поверхностью не контактирует. В такой облицовке устраивают технологические зазоры, через которые пар может беспрепятственно удаляться.
- Однако проблема выбора материала для такой отделки тоже существует, только связана уже не с паропроницаемостью. Любая кладка нуждается в ветрозащите, особенно однорядная - когда толщина стены формируется за счёт ширины газоблока, монтируемого в один ряд.
- У такой кладки швы хоть и тонкие, но не имеют внутренней перевязки, поэтому если где-то есть незаполненные клеем стыки, через них будет утекать тепло, ощущаться сквозняк. Такие швы, например, есть в кладке из пазогребневых блоков (по этой причине производители один за другим отказываются от них в пользу гладких).
- Не заполняются швы полностью и при монтаже газоблоков на клей ППУ, так что вопрос ветрозащиты требует пристального внимания. Проблема заключается в том, что не каждый материал эту самую ветрозащиту обеспечит – взять тот же виниловый или металлический сайдинг, который не только продувается, но ещё и гремит на ветру.
- Хорошим вариантом внешней отделки являются модульные панели керамосайдинга, стыки которого по периметру заполняются силиконовым герметиком. Такая облицовка долговечна, сейсмостойка, и даже обладает способностью самоочищения. Но она имеет существенный вес, из-за которого придётся использовать более плотные и прочные блоки, что делает стены более холодными.
- По этой же причине для отделки газобетонных домов не используют и керамогранит или крупные плиты натурального камня. На отечественном рынке есть немало предложений искусственного камня, монтируемого на подсистему. Но каркас ведь тоже крепится к газобетону, поэтому выбирать такой материал для отделки дома без расчёта нагрузок нельзя.
- Самым лучшим материалом для устройства вентилируемого фасада является керамический кирпич, так как он не требует подсистемы и опирается на фундамент. Важно только, чтобы такая отделка была предусмотрена ещё до начала строительства, а фундамент был рассчитан на её вес, и имел выступ для опоры лицевой кладки.
Схема газоблочной стены с кирпичной облицовкой
- Для притока воздуха в нижнем ряду кирпичной облицовки оставляют незаполненные раствором вертикальные швы (продухи), а для удаления пара, который поднимается вверх – технологический зазор между последним рядом и карнизом. Отступ между основной и декоративной кладкой составляет не менее 40 мм, что должно учитываться при определении ширины фундаментных лент и ростверков.
Кирпичная облицовка не только не препятствует выходу пара, но и является отличной ветрозащитой – не говоря уже о широких возможностях для дизайна фасада.
Нужна ли газобетонному дому теплоизоляция
Газобетон - материал в принципе самодостаточный, и если толщина стен рассчитана правильно, в утеплении не нуждается. Устройство внешнего теплоизоляционного контура может быть обусловлено двумя причинами: наличием моста холода в виде кирпичного или железобетонного армопояса, монолитных перемычек или колонн, либо исходя из соображений всё той же ветрозащиты.
- Выбирают утеплитель по тому же принципу, что и отделочный материал: он должен обладать более высокой паропроводимостью, чем газобетонная кладка. Утеплители на полимерной основе: плитные и напыляемые пенополистиролы и пенополиуретаны, являются плохим выбором.
- Они практически не пропускают пар, запечатывая его в толще стены - это вынуждает делать в помещениях дорогостоящую пароизоляцию, при том, что на 100% она всё равно не защищает. Утепление пенопластами нельзя выполнять сразу по окончании строительства.
Важно: В газобетоне есть и собственная влага, которой он напитывается в процессе автоклавной обработки, и нужно дождаться её снижения. Чтобы произвести утепление пенопластом, необходимо выждать минимум полгода, пока влажность газобетона с 30% не снизится до 8% - а такое время у застройщика есть не всегда.
- В качестве утеплителя лучше использовать базальтовую вату, которая не только обладает более высокой чем газобетон паропроницаемостью, но ещё и способна забирать у него часть влаги на себя. Главное - чтобы над поверхностью минваты был вентилируемый зазор, через который лишняя влага будет удаляться.
- Чаще всего утеплители используются в качестве основания под штукатурку, но могут для защиты от продувания закладываться под сайдинг. Некоторые умудряются монтировать пенопласт или минвату под кирпичную облицовку, но это вообще лишено смысла.
- Про пенопласт уже всё сказано: он запечатывает влагу в стене, и всякий смысл в устройстве вентзазора отпадает. При утеплении минватой таких проблем не возникает, но всё же она не сможет под кирпичной облицовкой так быстро избавляться от влаги, как это необходимо.
При повышенной влажности у неё снижаются теплоизоляционные свойства, она теряет объём и комкуется. И потом, срок службы у каменной ваты хоть и больше, чем у пенопласта, но меньше, чем у кирпича – а ведь чтобы заменить утеплитель, лицевую стенку не разберёшь.